Is there Foreign Object Management Program in YADA?
- Share
- Issue Time
- Jul 20,2024
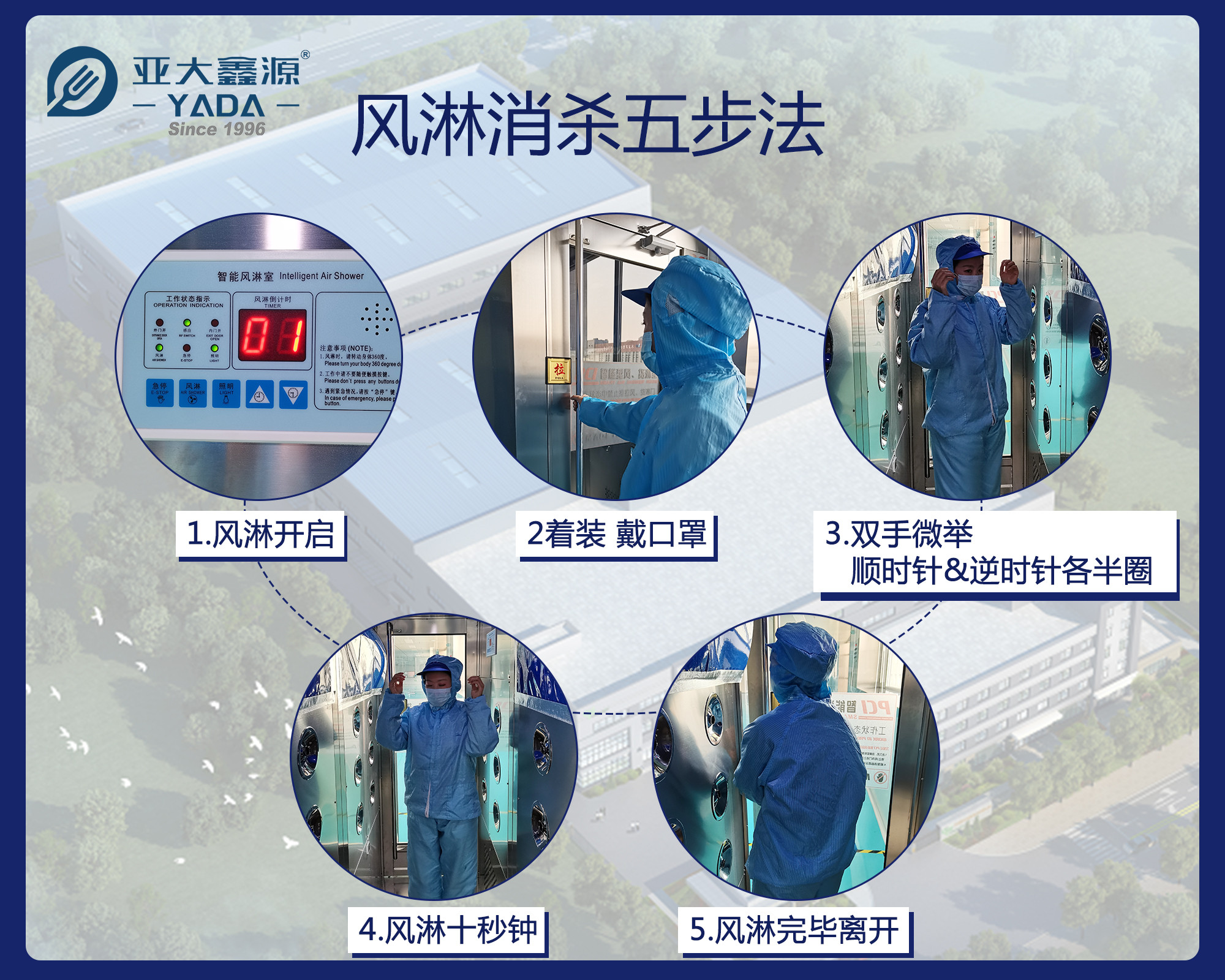
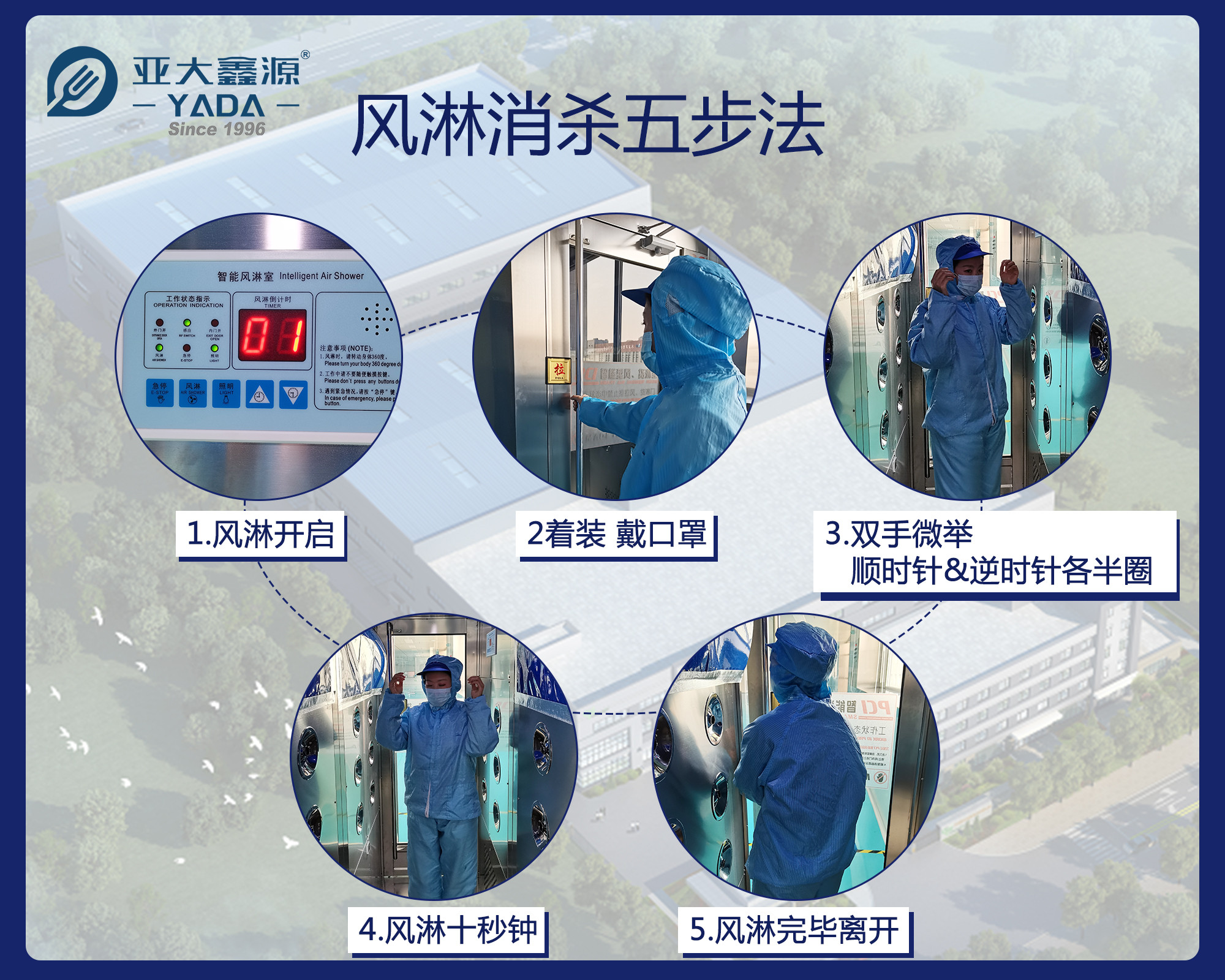
In order to prevent contamination of products by pollutants and to ensure the hygiene and safety of products, YADA Quality Department is responsible for proposing various factors that may contaminate the products, including equipment, facilities, workshop environment that may come into contact with the products, as well as other requirements for employees.
Walls, pillars and floors shall be non-toxic, non-permeable, and shall not contain dirt or erosion.
The ceiling should be non-toxic, white, waterproof, mildew-proof, non-shedding, and there should be no flaking, dust accumulation, dirt, erosion and other situations.
Workshop entrances, doors, windows and other apertures are equipped with insect and fly lamps. They should be cleaned and inspected regularly and recorded in the Monthly Hygiene Inspection Form.
Lighting facilities are equipped with explosion-proof lampshades or use explosion-proof lamps.
Drainage ditches are equipped with both open and concealed ditches. The size of the caliber of the drainage ditch can meet the smooth discharge of sewage; the drainage ditch pipe is solid, smooth, and does not seep; the ditch cover is made of durable, rust-resistant material. It should be cleaned and inspected regularly, and there should be no dirt, erosion, odor and other situations.
If the production workshop uses fragile tools such as glass, ceramics and fragile plastics, it should be registered and broken to prevent the products from being mixed into the products. It is strictly prohibited to bring non-production glass, bamboo, wood and other fragile products, employees' personal belongings and edible food or drinks into the workshop.
Tools and other sharp metal implements, including scissors, cutting blades, piercing blades, and wire used in manufacturing, are controlled if there is a risk of product contamination.
Available methods include, but are not limited to, the following:
Permanently secures tools to equipment to prevent loss.
Use the Item Issuance Cataloging and Registration Protocol to control items and complete the Sharps Receipt and Dispatch Record.
Prohibit the use of art knives with breakable blades.
Staples, paper clips and pins and wood products are not to be used in the product area.
If staples or other items are used as packaging or encapsulating materials, appropriate measures shall be taken to minimize product contamination.
The person in charge of each workshop shall check the integrity of sharps on a daily basis and fill in the "Record Sheet for Inspection of Glass, Rigid Plastics, Fragile Products and Foreign Objects" to prevent foreign objects such as sharps from mixing into the product and causing product contamination.