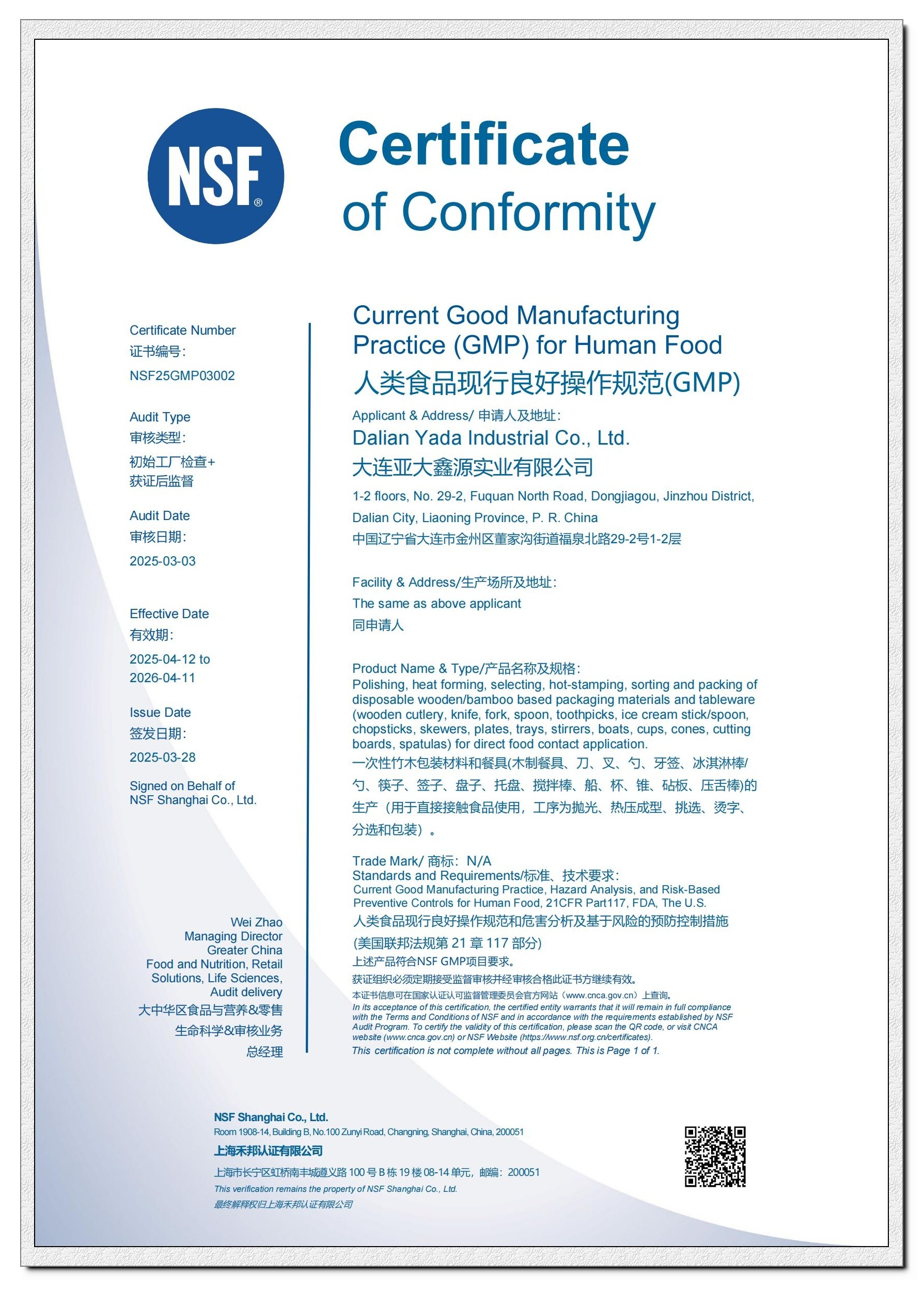
Current Good Manufacturing Practice (GMP) for Human Food
Item specifics
- Period
- 2025/4/12 - 2026/4/11
- No.
- NSF25GMP03002
- Certification bodies
- NSF Shanghai Co., Ltd.
Certificate description
What is GMP?
Good Manufacturing Practices, or GMP, represent a set of stringent and meticulously designed standards that govern the production processes in various industries to ensure the quality, safety, and consistency of the final products. These practices are particularly crucial in sectors such as food, pharmaceuticals, cosmetics, and medical devices, where product integrity is vital for consumer safety and efficacy.
GMP provide a framework that outlines the necessary conditions and parameters an operation must maintain to produce high-quality products reliably. The system covers everything from raw material procurement to final product delivery, ensuring each step meets specific quality criteria.
The quality management aspect of GMP focuses on establishing a culture of continual improvement within the manufacturing facility. It ensures that all employees understand their role in maintaining product quality and adhere to standard operating procedures (SOPs). This includes training programs, procedure manuals, and regular review of processes to identify areas for enhancement.
Sanitation and hygiene are critical in preventing product contamination and cross-contamination. GMP guidelines require rigorous cleaning and disinfection protocols for equipment, tools, and the production environment. Personal hygiene among personnel is also emphasized, including the use of proper attire, handwashing stations, and restrictions on eating and drinking in production areas.
Facilities and building requirements under GMP are designed to promote a clean, well-organized, and appropriately zoned working space. Manufacturing areas must be maintained at certain temperature and humidity levels, with airflow systems that minimize contamination risk. Equipment placement and workflow design should preventmix-ups and facilitate one-way traffic to avoid cross-contamination.
Equipment used in the manufacturing process must be designed for ease of cleaning and maintenance. Regular calibration and inspection of machinery are required to ensure it operates correctly and consistently, thus maintaining product quality. Equipment should be appropriate for its intended use, with smooth surfaces to prevent accumulation of debris and a design that allows for thorough cleaning.
Raw materials must meet strict specifications regarding identity, strength, quality, and composition. They should be stored properly to prevent degradation and must be traceable for lot accuracy. This ensures that any potentialquality issue can be quickly identified and contained, protecting both the consumer and the manufacturer’s reputation.
Personnel play a crucial role in GMP compliance. All staff must receive extensive training on GMP requirementsand their responsibilities within the system. There must be clear policies on work attire, personal hygiene, and behavior in production areas to prevent human error or contamination that could compromise product quality.
Validation and qualification activities confirm that processes, procedures, and equipment operate correctly and consistently deliver the desired results. Process validation involves detailed documentation of all critical steps in the manufacturing process, ensuring each can reliably produce quality products. Equipment qualification ensures machines perform accurately and consistently over time.
Effective complaint handling is integral to GMP, providing a mechanism for addressing customer issues and concerns. Complaints are thoroughly investigated and resolved, with appropriate corrective actions taken to addressany underlying quality issues.
Documentation and record-keeping are vital for demonstrating GMP compliance and facilitating regulatory audits. All aspects of the manufacturing process, from equipment maintenance to production batches, must be meticulously documented. Records must include accurate details of production runs, quality control checks, and any deviations or corrective actions taken.
Regular inspections and quality audits help maintain continuous compliance with GMP standards. Internal and external audits assess the effectiveness of the quality system, identifying areas for improvement and verifying that established procedures are followed consistently.
In summary, GMP are essential for ensuring that manufactured products are safe, effective, and of high quality. They provide a comprehensive blueprint for every step in the manufacturing process, from raw materials to finished goods, creating a culture of quality throughout the organization. Through meticulous planning, rigorous execution, and continual improvement, GMP serve as the backbone of quality assurance in manufacturing environments worldwide.
Good Manufacturing Practices or GMP is a system that consists of processes, procedures and documentation that ensures manufacturing products, such as food, cosmetics, and pharmaceutical goods, are consistently produced and controlled according to set quality standards. Implementing GMP can help cut down on losses and waste, avoid recall, seizure, fines and jail time. Overall, it protects both company and consumer from negative food safety events.
GMP examine and cover every aspect of the manufacturing process to guard against any risks that can be catastrophic for products, such as cross-contamination, adulteration, and mislabeling. Some areas that can influence the safety and quality of products that GMP guideline and regulation address are the following:
● Quality management
● Sanitation and hygiene
● Building and facilities
● Equipment
● Raw materials
● Personnel
● Validation and qualification
● Complaints
● Documentation and record keeping
● Inspections and quality audits
If you need to view the original document of our certificate, please contact us to obtain the download permission password.
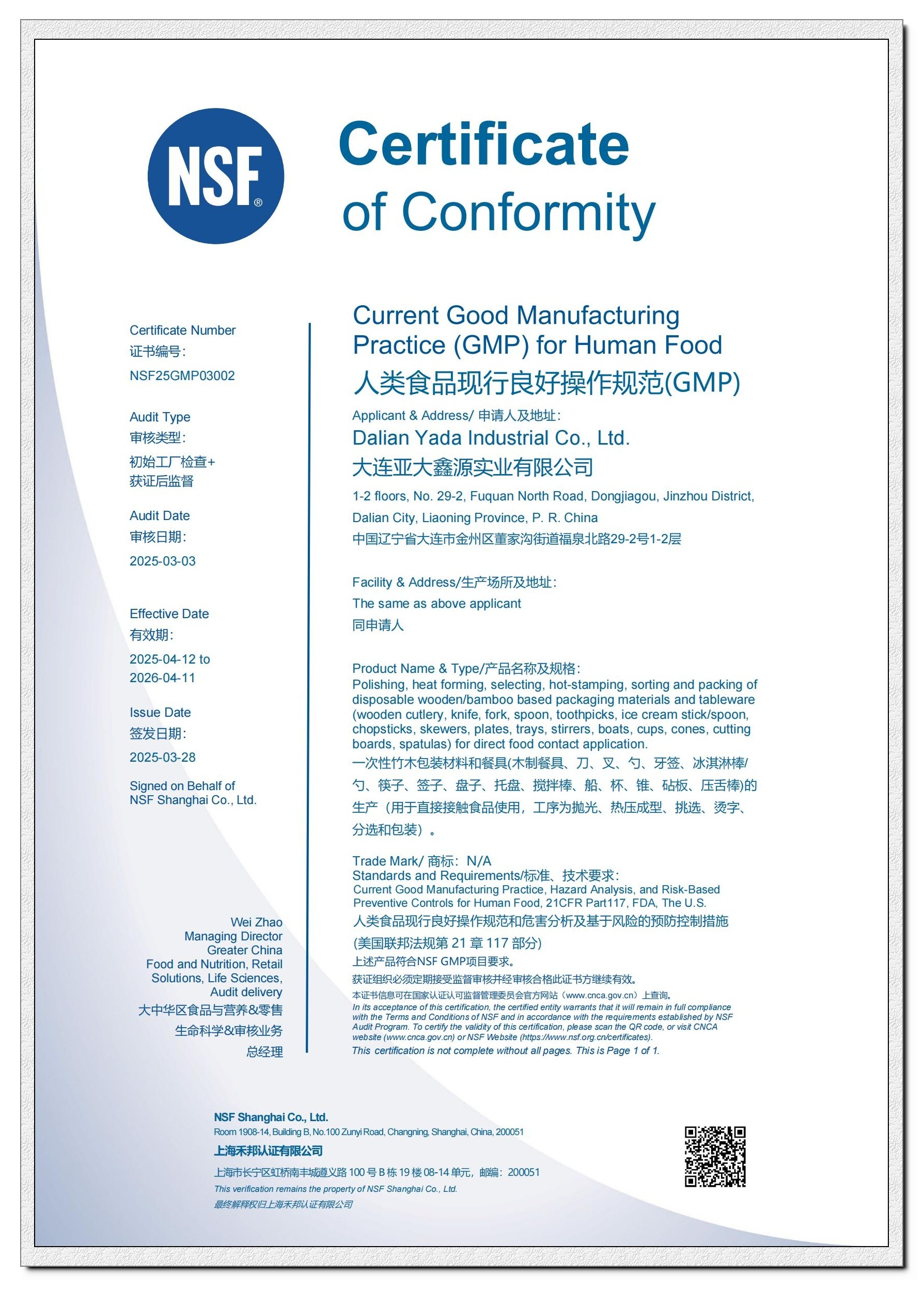